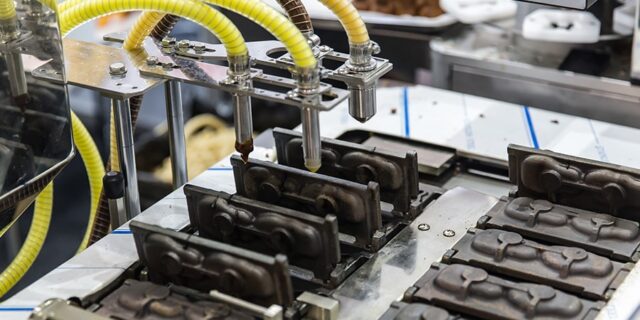
I spent many childhood hours assembling plastic models of cars, trucks, and airplanes. I always wondered how they made the tiny parts that would become my completed models. I eventually learned, as an adult, when I took a job at an injection mold manufacturing company.
Injection mold manufacturing is incredibly simple compared to more complex forms of manufacturing. And yet, it is an amazing process capable of accomplishing amazing things. I continue to be fascinated by what manufactures can create with a well-designed mold and a batch of molten plastic.
The Basics of Injection Molding
The basic premise of injection mold manufacturing is to inject molten plastic into a mold. The plastic cools very quickly. When you pop it out of the mold, it comes out in the shape of whatever the mold was designed to create. As for the molds, they are multi-piece steel molds made by skilled craftsmen.
Injection mold manufacturing is what made all those car and truck models I used to build as a child. Even today, the process is alive and well. It turns out plastic cups and dishes, parts for cars, plastic tools, ballpoint pens, and on and on.
It is an extremely easy process and one with built-in repeatability. That is key to manufacturing large volumes of parts at a low price point. You need repeatable processes that continually turn out one identical part after another. Injection mold manufacturing does just that.
Dealing With the Cutoffs
On my very first day on the job, I was put on a machine that was spitting out arm pieces for sunglasses. Each mold ejection yielded a large plastic frame to which eight arms were attached. My job was to cut the arms off and then trim any excess plastic to ensure they were smooth. The larger frames from which the arms were cut were known as cutoffs.
All of us machine operators threw our cutoffs into large steel bins on wheels. When a bin was filled up, we called for a new one. Someone from the warehouse would come to exchange an empty bin for the full one. What happened to the cutoffs? They were picked up by a recycling company.
Turned Into New Material
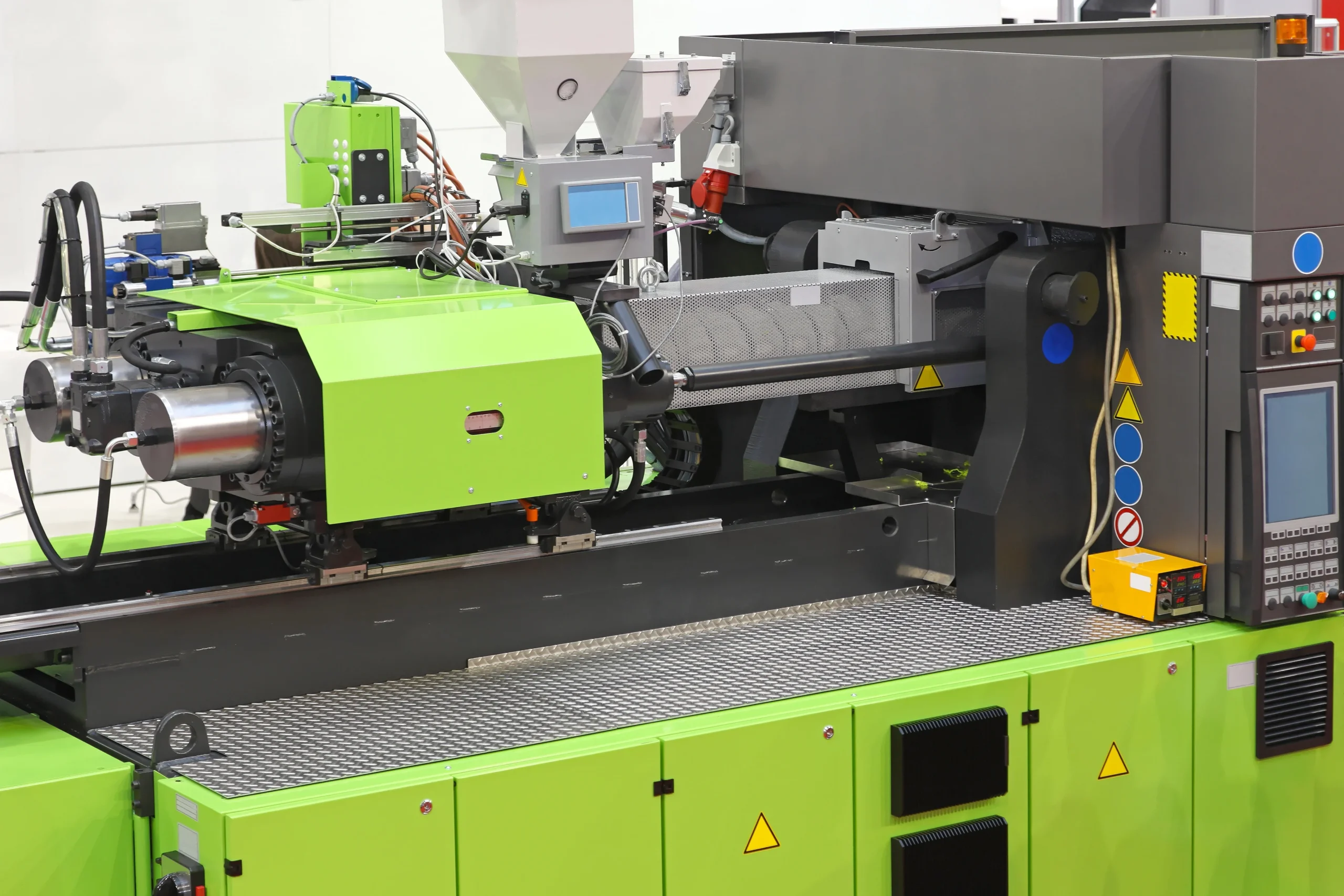
It has been so long that I do not remember the name of the recycling company that purchased the cutoffs. But Tennessee-based Seraphim Plastics pretty much does the same thing today. They purchase plastic cutoffs, injection mold machine purge, and other types of industrial plastic scrap from companies in seven states.
What do they do with it? They turn it into a new material known as regrind. All the scrap they purchase gets run through a series of grinders that reduce it to small pellets. Manufacturers buy those pellets, mix them with virgin plastic pellets, and inject the mixture into molds to create new parts.
Hundreds of Pieces Per Minute
That very first injection mold machine I worked on was capable of pushing out hundreds of pieces every minute. The fascinating thing was that my machine was one of the smaller ones in the factory. There were larger machines pushing out thousands of pieces to my hundreds. And every single piece was identical to every other piece before and after it.
If you have ever wondered why manufacturers love plastic so much, the simplicity and repeatability of injection mold manufacturing explains it. Thanks to injection molding, manufactures are able to churn out incredibly large volumes of pieces at a very low cost. We benefit by way of lower prices at retail. What is not to love?