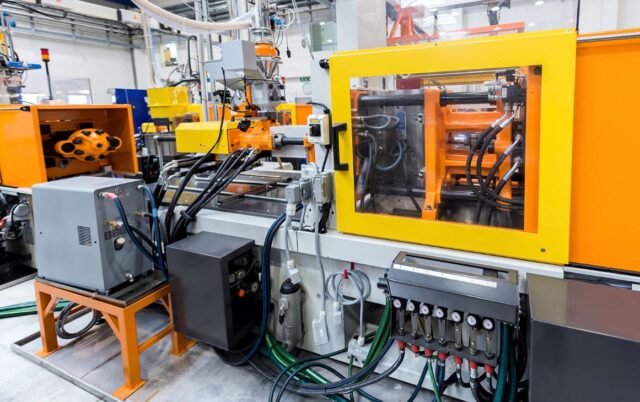
Injection molding is a manufacturing process that has been around for more than one hundred years. It may well be one of the manufacturing processes for producing the same item thousands or even millions of times. This is why many companies like to work with this process. Once you set up the machine to start creating a certain item, you won’t have to do any kind of change to it even after it goes through thousands of cycles.
What’s even more interesting about injection molding is that it can be used with all kinds of materials. Whether you want to produce a product from plastic or metal, it can be done. It truly is an amazing technique that can be applied for any kind of production.
However, plastic is still the number one most common material used with this type of manufacturing. It is the most popular option because it is reliable and simple to work with, but it is also very cost-efficient. Sure, aluminum, steel, or other metals may be much more durable, but manipulating this type of material is much more complicated which requires expensive machinery.
The term plastic has a much wider meaning than what most people think. It usually refers to all kinds of synthetic organic compounds than have high amounts of malleability. To be malleable means that the item can go under a high load of compressive stress without deformation.
So, you are now probably wondering about which plastic materials are the most popular in the injection molding industry. Well, here are some of them.
ABS or Acrylonitrile butadiene styrene
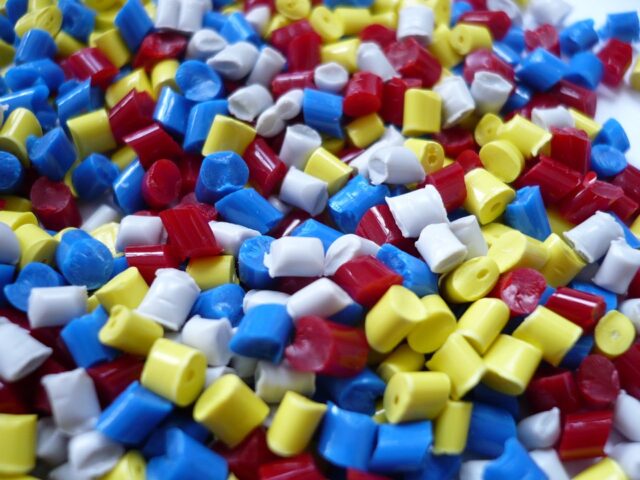
If you were to ask any company in this industry about the strongest plastic material used in this manufacturing process, everyone will answer with ABS. Acrylonitrile Butadiene Styrene is the one with the highest amount of toughness, strength, and temperature resistance out of the bunch. It truly is everything that you would need in a high-quality product.
It is also quite malleable, flexible, and light which means that it can basically be turned into anything that you want. Additional modifications can be made to the ABS to boost its other properties such as its toughness or resistance to heat. It truly is a remarkable material that should be considered as everyone’s first option.
ABS has an application in almost every industry that you can think of. It is used by the automotive industry for pipes and other parts that are a must-have for every vehicle. ABS can also be found on airplanes, boats, trains, and other huge transportation vehicles.
Believe it or not, but ABS also has the most basic applications. You probably have contact with ABS every single day without you ever knowing. For example, a computer or a phone with which you are reading this article probably has a couple of parts made out of Acrylonitrile Butadiene Styrene. The toys that your kids are playing with are also made out of ABS.
The only disadvantage to ABS is the fact that it does not have good chemical resistance. It should never be used for storing chemicals, insulation, etc.
Acetal
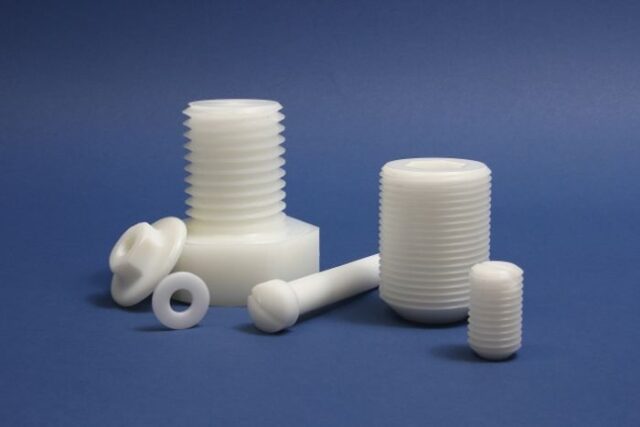
Polyoxymethylene or acetal is a thermoplastic that has great stability and provides very low friction which is perfect for the automotive and the airplane industry. Acetal is the number one choice for companies that are looking to create springs, screws, nuts, pump parts, mechanical gears, etc.
However, acetal has a lot of uses outside of these markets too. For example, most of the companies that manufacture containers for food and for beverages prefer to use polyoxymethylene. It does not release any kind of toxins which makes it safe for both humans and animals too. If you are looking for plastic mold makers that work with this kind of material, you should check out Moldall.
Another fun fact about Acetal is that it is used to create paintball guns and all of the accessories that come with these “toys”. Its durability is the best choice for creating something that will undergo a lot of air pressure during its lifetime.
Polyethylene
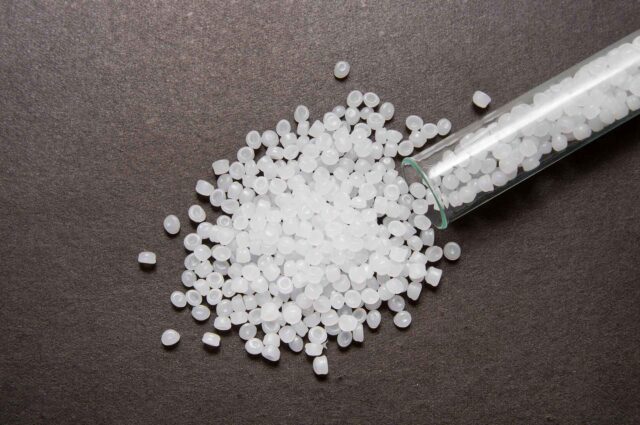
While Acetal and ABS seem like plastics without any kind of disadvantages, they still are not the best most popular type of material used in the injection molding industry. Why wouldn’t everyone want to use those two when they obviously have great structural properties? Well, the answer is actually quite simple. They are expensive.
Of course, every company wants their product to have the highest possible quality, but when you need to manufacture millions of that same product, it can get expensive to use Polyoxymethylene or ABS. This is where the most common plastic used today comes into play. Polyethylene has pretty low rigidity and hardness when compared with some other materials, but it has high ductility properties. This means they can endure a lot of pressure without ever getting damaged.
This is another type of plastic that you get in contact with every single day. It is used for manufacturing containers such as bottles, plastic bags, and different kinds of packaging.
While Polyethylene is a great and cheap option for the most company, its biggest advantage is the waste it leaves behind itself. Billions of people throw polyethylene products away without recycling. This is why managing waste from polyethylene is almost impossible. The number of items made out of this material is simply too high.
Polycarbonate
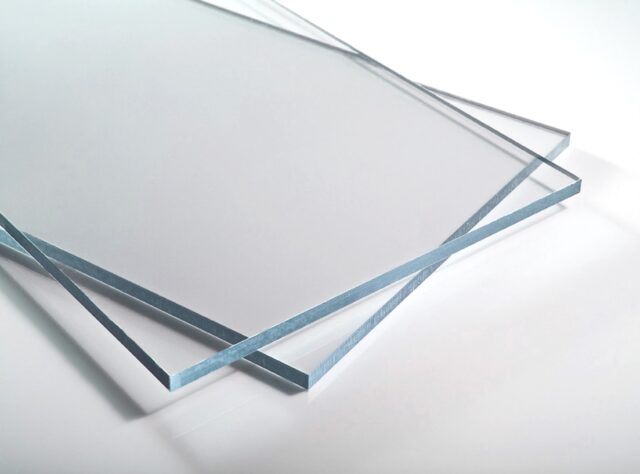
Polycarbonate is a quite tough and strong material and it is usually transparent. It can easily be formed into any kind of form which is why it has a lot of applications.
Polycarbonate is a great electric insulator which is why it is used in all kinds of electric devices such as phones, computers, cars, etc.
Because of its transparent properties, it is also used in the construction industry for greenhouses, sound walls, etc.
Nylon or Polyamide
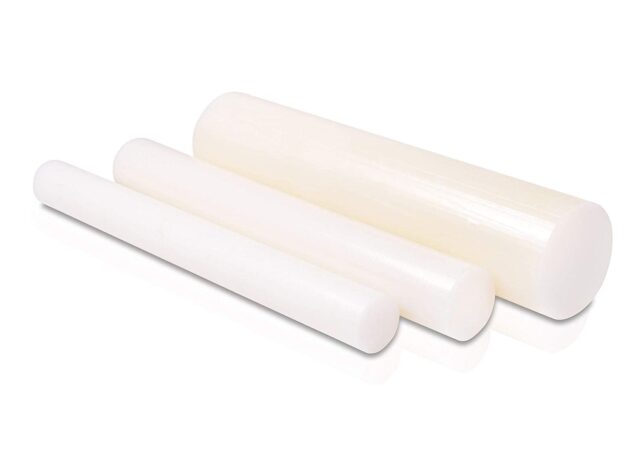
Nylon has very high stability and is very resistant to chemicals and impact. You will find the use of nylon in a lot of products such as footwear, clothing, protective equipment, and even medical products. It has also seen a fair use for wrapping all kinds of meat and even for cooking because it has very high-temperature resistance.
The disadvantage of using nylon is the fact that it takes thirty to forty years to decompose, leaving a lot of toxic waste.
All of these plastics we mentioned above have millions of different usages every single day. Keep in mind, there are many others that have different kinds of properties and usages.